
Set up copper pours on top and bottom and connect to ground plane (although sometimes I'll have a power plane on top if I have multiple positive voltages)ĩ. After layout and routing, when I'm happpy where everything is, I rotate or move the component labels for the silkscreen.Ĩ. I use DipTrace's alignment and spacing options a lot to get things nice and balanced in each column.ħ. I aim for some degree of symmetry where possible but do not possess Mr. When I'm laying out components I try to take many leaves from our good proprietor's book and attempt to put runs of resistors in an inner column along either side of the ICs with caps in outer columns, at least where possible. I try and route horizontal traces on the top layer and vertical traces on the back and connect these by vias if necessary for tricky sections (I think I read it's called Manhattan routing?)Ħ. I always hand-route, although i will sometimes run the autotracer to get ideas about tricky parts. I used to do layout and tracing as distinct steps but I found it worked less well and I have a bunch of aborted layouts from that time. I usually get better results if I do traces as I lay out the components, although there is still a lot of stuffing around re-working traces if you do it that way. I ignore the ground net, as I use copper pours as ground planes.

I dont care much about the schematic or ratlines at this stage, just the nets. I then highlight each net, lay the compnents from it out on the board and add the traces. Some people use thicker traces here (0.33 mm) for heat dissipation on the power path and thinner ones (0.2 mm) for the audio paths.ĥ. Go through the schematic and firstly complete the LED path and the power paths. Pads for 3PDT, DC and jack ground are on 2.54 mm centre spacing so that screw terminal blocks can be used if desired.Ĥ.


I also place things like ICs centrally and evenly spaced from each other too. I always specify an exact location for these rather than dragging or using the dimension tool, which I find inaccurate and messy. pots, switches, DC input, 3PDT breakout pads etc).
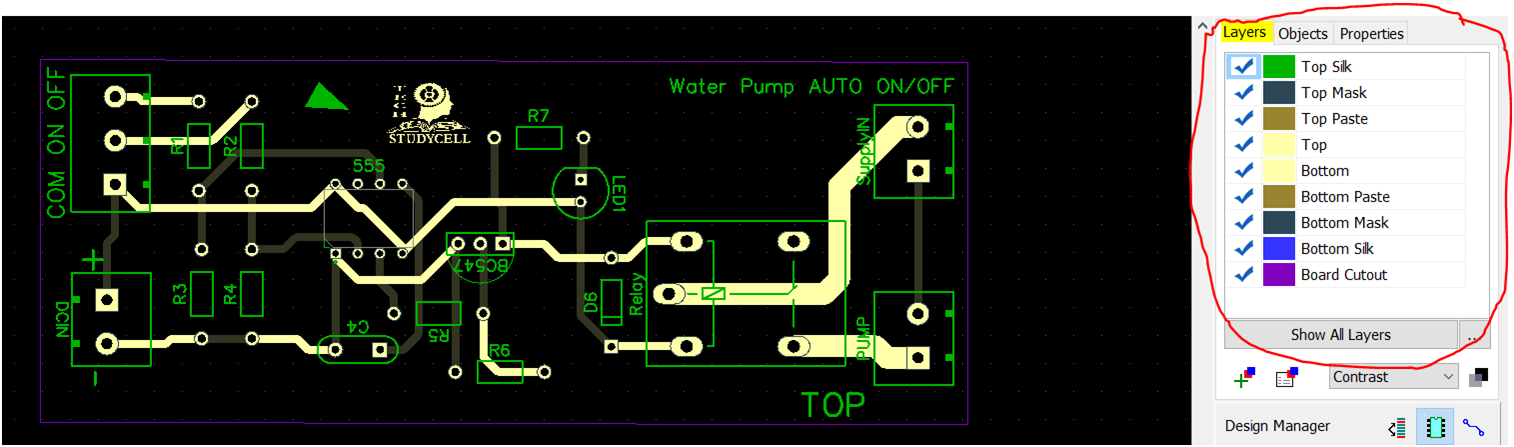
Lay out hardware that must correspond to an external drill hole or component (e.g. Place the template so that the origin is in the centre, which helps me line things up perfectly with my Illustrator designs.ģ. Then I place the proper board over it at the end.Ģ. I find it easier to do this with a rectangle, in case i want to alter the dimensions of the board easily during the layout process. Not sure if these are best practice, but my workflow is something like this:Ģ.
